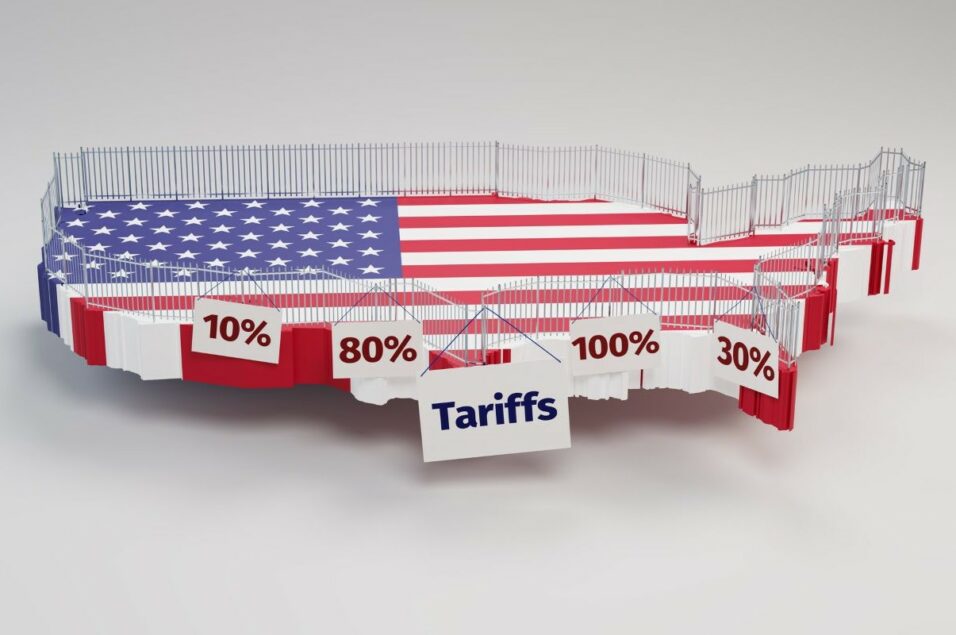
Manufacturing and industrial executives today are operating in an environment rife with uncertainty. They must track multiple risks and opportunities, assess potential impacts, and make rapid decisions to keep on course. The latest tariff policy shifts, which are disrupting supply chains and driving economic volatility, are flashing warnings that require immediate attention.
Competitive positioning remains a key focus. Companies are monitoring how rivals are adjusting their supply chains, pricing strategies, and automation investments to mitigate cost increases. Meanwhile, macroeconomic volatility, including the effects of inflation, interest rates and shifting consumer demand, is influencing investment and profitability. Many executives are also tracking government incentives, reshoring programs, and tax policies that could create opportunities for domestic expansion and modernization.
While all of these factors demand attention, certain risks stand out as immediate priorities. Tariff decisions and trade policies, particularly in sectors reliant on steel, aluminum, industrial electronics and automotive supply chains, are a top concern.
The looming uncertainty around trade with Mexico and Canada adds complexity. An integrated North American supply chain is essential to automotive and heavy-equipment manufacturing. Any tariff increases on imports from these nations could result in higher production costs, inefficiencies in logistics, and increased working capital tied up in extended cycle times.
Broader macroeconomic trends are also shaping decision-making. Tariffs contribute to inflation, which in turn affects borrowing costs and capital investment. Supply chain disruptions, whether from increased duties or logistical bottlenecks, can further complicate procurement and production planning. At the same time, companies must consider how end-market demand will react to tariff-driven price increases, as weakened demand could compound the financial strain.
To mitigate the impact of these risks, manufacturers are actively deploying a range of countermeasures. Some are looking to reconfigure their supply chains, adjusting final assembly locations to qualify for lower tariff rates, or engaging in tariff engineering by modifying product classifications. Others are exploring opportunities to take advantage of free trade agreements that can minimize exposure to duties on key materials.
Competitive intelligence has become an essential tool in this environment. Organizations are closely watching how rivals respond to cost pressures, whether by passing them along to customers, absorbing them, or investing in automation to offset increased expenses. Understanding competitor strategies is critical to maintaining market position.
Pricing strategy is another area of concern. Some industries have greater flexibility to pass tariff costs on to customers, while others are likely to face greater resistance. Companies are analyzing factors such as demand elasticity, competitor pricing and existing customer contracts that may limit their ability to implement changes. For many, the choice comes down to absorbing costs, restructuring supply chains or finding efficiencies elsewhere to maintain profitability.
While these concerns dominate executive attention, several risks remain underappreciated. One of the most overlooked areas is the potential for retaliatory tariffs from key trading partners. While U.S. tariff policies have been widely discussed, less attention has been given to countermeasures from China, the European Union and North American allies. Such actions could disrupt exports of U.S. aerospace, high-tech and agricultural products.
Also frequently overlooked is the potential for missed opportunities. Companies are focused on avoiding tariff-related costs, but might not be fully capitalizing on government incentives for domestic manufacturing. With reshoring incentives, tax credits and infrastructure investments on the rise, those that position themselves for these programs could gain strategic advantage.
Supplier consolidation and capacity constraints present hidden risks. While some companies are shifting suppliers to avoid tariffs, they might not be fully assessing whether new partners have the capacity to handle increased demand, or whether logistical trade-offs will erode anticipated savings. Failure to properly vet alternative suppliers can create bottlenecks and vulnerabilities that lead to additional disruptions.
The visible hand of government intervention is reshaping industrial manufacturing, and executives must take a proactive approach to managing risk and capitalizing on opportunities. By closely monitoring key indicators, implementing strategic adjustments, and anticipating both threats and advantages, they can navigate today’s uncertainty with confidence.
Matthew Lekstutis is a supply chain and procurement consultant with Efficio.