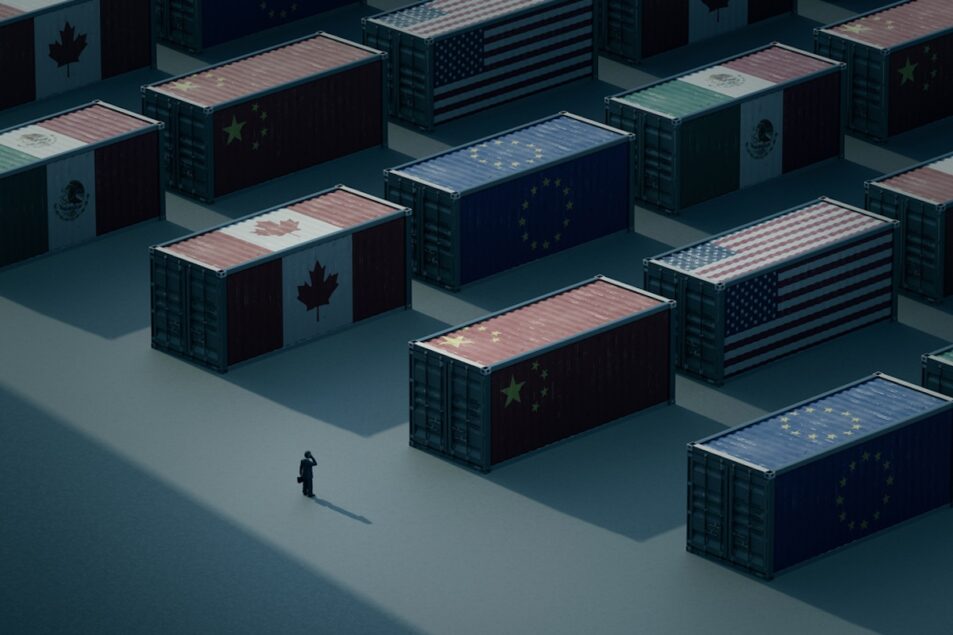
As of mid-April of this year, the U.S. had imposed or threatened tariffs on a wide range of goods, including 25% on many imports from Canada and Mexico, 145% on all Chinese imports, and a global 25% on aluminum and steel. In response, Canada, Mexico, the European Union, and China introduced retaliatory tariffs.
Tariff policies under the new Trump administration have changed rapidly. Initially, the 25% tariffs with Mexico and Canada applied to all goods. Two days later, they were limited to goods that don’t fall under the United States-Mexico-Canada Agreement (USMCA). Additionally, the U.S. briefly imposed a 50% tariff on Canadian steel, before reducing it to 25%, after Canada removed a retaliatory excise tax on energy exports. There were also unspecified agricultural and automotive tariffs potentially set for April.
The situation is unpredictable, to say the least, and it’s difficult to foresee how tariff policy will evolve over the coming months. But as potentially disruptive as they are, the tariffs also present an opportunity for companies to grow, and emerge even stronger from the current situation. Manufacturers need to build on the lessons they learned from the COVID-19 pandemic to innovate, adapt, and explore new strategies to remain competitive and resilient in the global market.
For starters, tariffs will significantly increase the cost of inventory, especially for parts and raw materials that aren’t widely available in the U.S. If they stay in place for an extended time, many suppliers will establish operations inside the country, which should bring prices down. In other cases, the price increases may be permanent, especially for raw materials that aren’t abundant in America.
In the near term, the tariffs could cause shortages when raw-materials suppliers in areas not affected by tariffs get hit by heavy demand. This sudden uptick could stretch lead times, causing further shortages and disruptions down the line. Many manufacturers are already stockpiling materials in anticipation of further price increases and supply chain disruptions.
Past trade agreements have resulted in the supply chains between the U.S., Mexico and Canada to become highly integrated. Products and components in various stages of completion are traveling across borders multiple times, compounding the tariffs’ effects. Decoupling and streamlining these supply chains will require a great deal of time and investment, and many companies may wait to see whether the tariffs will remain in place or the long term before taking drastic measures.
The industry has recently persevered through an analogous situation. The COVID-19 pandemic saw wide swings in demand, sudden shortages of raw materials and rapid changes in pricing. The lessons that manufacturers learned during that time will serve them well now.
To navigate the changing landscape of global tariffs, manufacturers must gain as much agility as they can. Technology can help, not just in the immediate term but also in setting up companies for even greater success once the trade disputes are resolved. Following are some recommendations for applications that can provide the flexibility and insights needed for management to adapt quickly to rapidly changing conditions.
Supplier relationship management. Manufacturers will need to source raw materials from a wider array of suppliers, within a reasonable timeframe. However, multi-sourcing can become very complex, very quickly. Artificial intelligence and machine learning should be employed to automate the process. Manufacturers who do so will be able to more rapidly find suppliers that can provide faster delivery at lower price points.
Predictive analytics and AI for inventory optimization and demand forecasting. Just as it was during the pandemic, visibility is vital for navigating the changing tariff situation. Predictive analytics and AI can crunch internal and external data to identify potential inventory shortfalls long before they become problems, enabling management to take proactive measures. They can also help manufacturers avoid becoming overcautious and ordering more raw materials than are necessary.
No manufacturer wants to find itself unable to fulfill orders or, conversely, have product sitting in the warehouse without any buyers. Predictive AI can supercharge demand forecasting, providing critical insights that can be used to guide production schedules.
Flexible production and operations. Insights are of little use if manufacturers can’t act on them. Raw material shortages may appear suddenly, especially in the early days of the tariffs. Technologies for enabling management to explore “what-if” scenarios, and systems that can reschedule production schedules around shortages. can prove critical to keeping facilities productive.
Quality management. Especially when buying from new suppliers — as many manufacturers will need to do if the tariffs remain in effect for an extended period of time — product quality becomes even more critical. Manufacturers will need to avoid raw materials that prove substandard, and factor that into their supply chain strategy.
The new tariffs bring opportunities for growth and innovation, encouraging manufacturers to embrace advanced technologies such as supplier management, predictive analytics, flexible operations, and quality control systems. By building on the lessons during the COVID-19 pandemic, companies can not only overcome these changes, but also more strongly position themselves for long-term success in a dynamic trade environment.
Kevin Bell is senior vice president of business development with SYSPRO.